A lot has been said and heard about Industry 4.0, and how it has transmogrify the manufacturing industry by allowing manufacturers with options to utilize new tools and technologies in the product life cycle. Most of us are aware that Industry 4.0 has allowed manufacturers to increase operational visibility, reduce costs, speed up production times, and deliver exceptional customer support.
Nevertheless, 2021 swiftly approaches, and the world is now moving towards Industry 5.0. it’s time to shift our attention away from Industry 4.0 and toward Industry 5.0. The fourth industrial revolution focused on using technology to optimize the means of production, the fifth is all about approximating man and machine — that is, a collaboration between humans and smart systems. Depending on who you ask, Industry 5.0 is either on the immediate horizon, or it’s already here, its arrival accelerated by the onset of the COVID-19 pandemic.
Regardless of the viewpoint, you subscribe to, there are often little questions that manufacturers must still embrace change so as to remain before competitors and win market share in an ever-evolving industry. Those who wish to not just survive, but thrive, must leverage the newest technologies and trends.
VR & AR Support Touchless Service Model
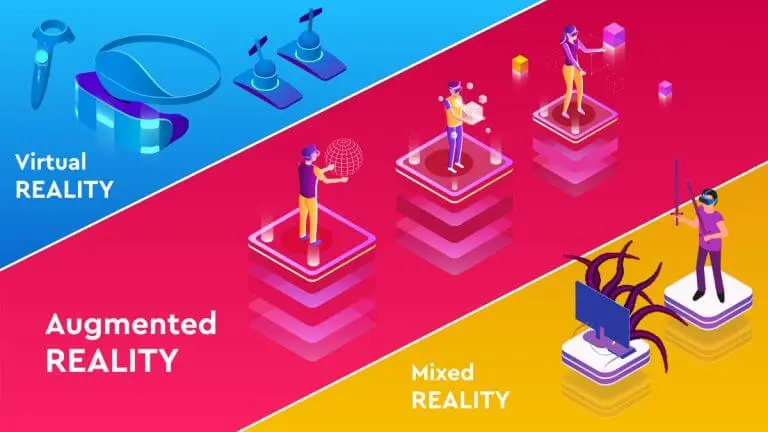
COVID-19 has been the major hindrance in the field of service arms of manufacturing companies, intercepting technicians from visiting job sites to install equipment or supervising repairs. Luckily, hard-wearing technology such as augmented reality (AR) and virtual reality (VR) has made it possible for technicians to provide remote assistance by sending customers AR- and VR-enabled devices and walking them through basic troubleshooting and repairs.
For manufacturers, this acted as an exhilarant opportunity. In the past, customers were often reluctant to explore touchless service options and instead preferred the convenience of getting a technician to come onsite to finish a repair. Now, thanks to COVID-19, more customers are hospitable to this concept, enabling manufacturers to gauge new processes and procedures with the long-term goal of creating them permanent fixtures. In the end, customers and field service technicians enjoy the reduced risk of exposure, and makers enjoy exploring new lines of business from the reduced risk of exposure, and manufacturers benefit from exploring new lines of business.
IoT is (Still) The Big Thing
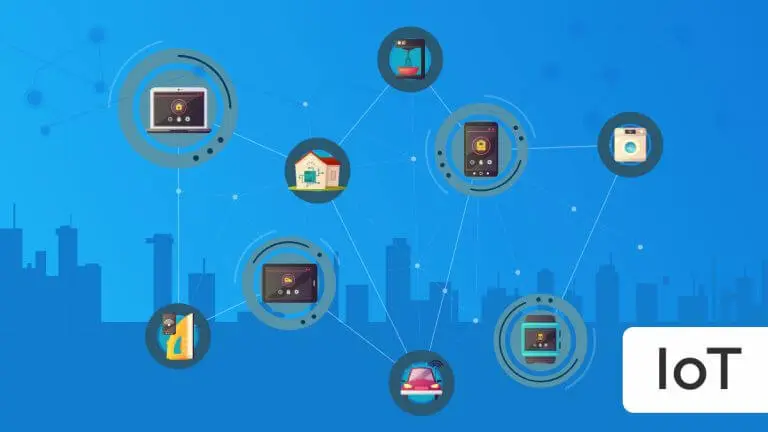
The Internet of Things (IoT) is becoming popular day by day, the widespread use of technology in the manufacturing industry, it remains at the top of trends lists year after year for its adaptability and innovation — and this year is no exception.
IoT, which allows the interconnection of unique devices within an existing internet infrastructure, has enabled manufacturers to make informed, strategic decisions using real-time data and achieve a wide variety of goals, including cost reduction, enhanced efficiency, improved safety, product innovation, and more. According to a study from the MPI Group, nearly a third (31%) of production processes now incorporate smart devices and embedded intelligence. Additionally, 34% of manufacturers have plans to incorporate IoT technology into their processes, while 32% plan to embed IoT technology into their products.
Intrinsic Security
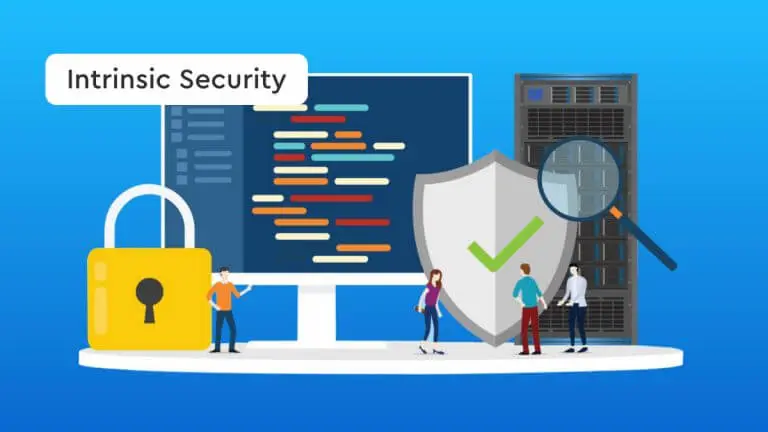
For the longest time, the technology world followed a bolted-on approach to security that mainly consisted of patching the infrastructure from the data center to the edge. With the risk landscape getting increasingly complex and sophisticated with the bad actors getting more sophisticated, it is now quite clear that this is not working. Security needs to be reinvented from the current model to be intrinsically built into every aspect of the infrastructure and applications deployed on it, thereby reducing the attack surface significantly.
The focus is on “known good behaviour” that can be used to detect anomalies which can then be isolated and addressed. AI/ML will form the underpinnings of this intrinsic security model and I believe the future of intelligent security will lie in how intrinsic security strategies operate in the context of infrastructure.
5G
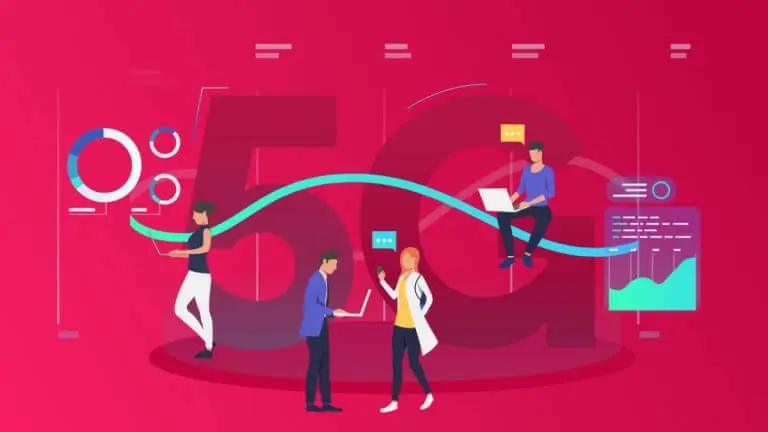
5G is going to be a game changer for the telecom sector. GSMA Intelligence forecasts that there will be more than 50 5G networks worldwide by 2021 and by 2025, there will be more than 1.3B 5G connections covering 40% of the global population.
From smart cities to connected healthcare to better security, there are innumerable use cases for 5G. Of course, delivering modern applications and services requires an agile and scalable telco cloud and a multi-cloud strategy that can unify your network and IT environments, and connect them to private enterprise clouds, edge clouds, and public clouds. As the network grows, AI will be the mechanism to simplify the complexity that will inevitably arise out of countless endpoints and unprecedented volumes of data.
Digital Connectivity To All The Things
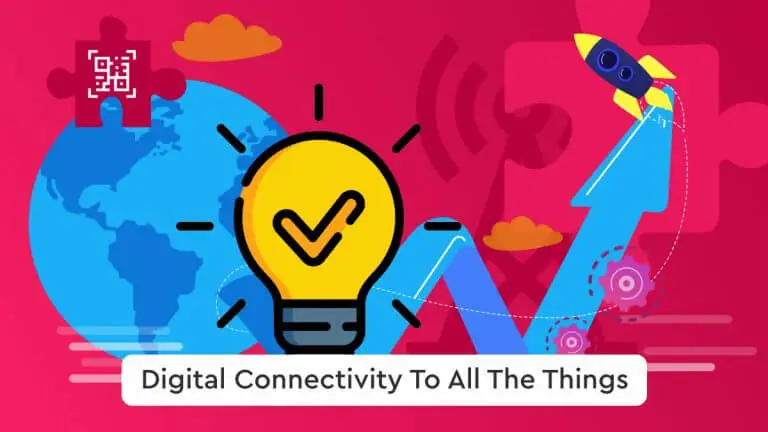
In 2020, the manufacturing and food processing industries were badly jolted by the global pandemic. From closed facilities to rigid communication channels, it was difficult for some to remain flexible. As a result, 94% of Fortune 1000 companies experienced disruptions in their supply chain.
In this year 2021, digital connectivity is going to be one of the imperious trends in manufacturing and food processing. Businesses will be looking to digitally connect as many prospects of the production process as possible to stay ahead of further disruptions.
They’ll do so by adopting tools that connect:
- Operations
- Inventory
- Employees
- Equipment
- Customers
It’s estimated that by 2025, over 75 billion manufacturing devices will be connected and communicating with each other.